Know the importance of natural castor oil in the industrial and automotive paint business
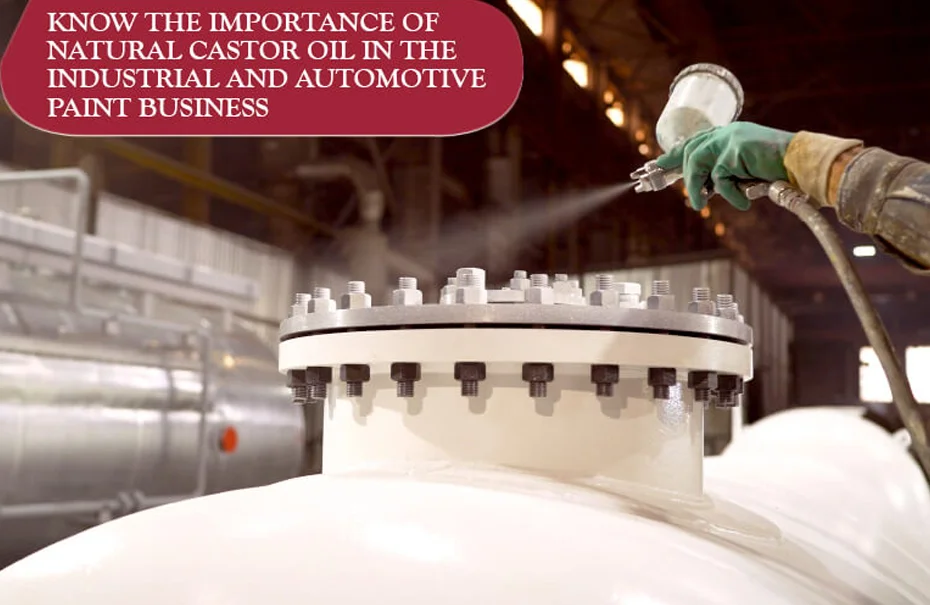
Natural castor oil has been hogging limelight owing to its lower toxicity towards mankind in general. Lowly priced automotive paints derived from castor oil have grossly replaced plasticizer materials.
Castor oil blended paints have taken over due to their easy availability worldwide, the biodegradability factor, and environment-friendly nature.
Polymer derived oils have applications in surface coatings, paints, and adhesives. The endeavor of this blog is to cast light on castor oil applications in the polymeric activities in recent times.
Emphasis is to be placed on drying oil applications in Industrial Automotive Paints.
The history of paints
Here are the several components of paints:
Pigments:
They’re broadly classified into organic, inorganic, and earth paints.
The coloration can be whites, metallic hues, or even vibrant colors. They are blended in desired proportions to get the perfect sheen and finish. The blending does affect toughness, durability, and several physical properties of coloration and coating.
Binders:
Paints have binders. They form a dry coating and adhere to the surface to be painted. Binders have polymeric substances, resins, and drying oil which function to provide gloss and firmness.
Solvents:
Solvents do maintain the liquidity of paints. This is done so the application, flexibility, and brush ability remains smooth.
The petroleum distillate ‘white spirit’ comprising salicylic, aliphatic & aromatic hydrocarbons was introduced in the paint industry. At first, it was regarded as cheap, but slowly by busting many myths, it started to garner praises.
Additives:
Additives impart special properties to paints. But, they’re found in paints in very low concentrations.
The additives components include driers, anti-skinning agents, thickeners, biocides, plasticizers, surfactants, antifoam agents, dispersing agents & catalysts.
The basics of paints
Paints are resin pigments with compatible pigments, additives, and solvents. Their useful applications to substrate surfaces form protective films. During ancient times, paint was a derivative of egg-shells, plant-extracts, mineral rocks, resins, and water is the most common solvent.
As modern technology ushered in, the present generation saw a humongous improvement in the quality of paints.
Modern paints are prepared to accommodate shape (amorphous to the transition crystalline), size (micron to the transition nano), dispersion stability, good looks, film-uniformity, and much more. The required durability has been achieved to obtain a smooth finish for exterior and interior purposes in automotive vehicles.
How castor oil manufacturers came into the light?
The use of harsh plasticizers degrades the environment at large. Modern Environment Regulation Act has been advising to reduce solvent emission. The use of conventional things for manufacture release green-house gases, thereby, posing the threat called global warming.
This is where natural castor oil has a huge part to play. This film-forming oil has applications in decorative, lubricants, and surface coatings. The plant (Ricinus communis) is harvested throughout tropical areas of India and certain parts of Africa. This spring plant has a natural greenish or reddish-purple coloration.
Certain more crucial facts
Castor oil has ricinoleic-acid (a monosaturated compound). Its structure has 18-carbon fatty acids having a hydroxyl-group on the twelfth carbon making it a similar derivative like that of resin.
This drying oil achieving cross-linking on being exposed to oxygen forms a solidified film. It is this property of natural castor oil that makes it a unique product in the automotive industry.
The research
Research says castor oil is incomparable as a chemical product & finds use in cosmetics and coatings.
Methodology to convert castor oil into plasticized paint:
The essential equipment used are as follows:
- The stopwatch
- Leveling cup
- Refractometer
- Viscometer cup
- The Hegman gauge
- Water bath
- Soxhlet extraction set
- Thermometer
- Heating arrangement
- Stirrer &
- Mild paints and applicators
The materials used:
- Rutile titanium-dioxide pigments
- Xylene white-spirit
- Resin
- Nitrocellulose &
- Castor seed
The process
- After obtaining the castor seeds, their shells are removed.
- The soft extracts are weighed carefully. They are gently heated to get rid of the moisture.
- Now, the seed extracts are re-weighed
- The oil extraction is performed at 200-250 degrees centigrade (approximately) using the Soxhlet extractor.
- Petroleum ether is used as the solvent. The viscosity of the oil was measured carefully using the Ford-cup-B-4 at normal temperatures.
- A stopwatch has to be used to check the time of flow-resistance of the oil.
Now, the specific gravity, the most important part is to be calculated. It is done under 1-atmospheric pressure. The expression obtained was as follows –
Specific Gravity (SG) – Weight of sample oil/Weight of water
The refractive index was to be recorded immediately using Abbe-refractometer.
Here, the boiling point was calculated minutely using a thermometer of capacity – 0-300 degrees centigrade.
The topcoat of the paint was designed in the following three important stages:
The Milling Stage:
This involves the grinding & dispersion of 20 percent (by weight) of rutile titanium-dioxide pigments in 80 millilitres of ceramic mortar & pestle.
The grinding process continues for an hour.
In the meantime, the test for the fineness of the pigment was determined by the use of Hegman-Gauge of 1-5 micrometres.
Stabilization Stage:
Here, the temperature plays a crucial part. The temperature of the paint dispersed is maintained at 26-27 degrees centigrade by adding 80 millilitres into the mix.
The mix is stirred with vigor to increase the inter-molecular space to hinder the aggregation of constituent particles. Now, around 250 millilitres of resin is put to the blend to ensure the good quality of the paint.
Let-down stage:
The stage is relatively simpler. It just needs the incorporation of additives like nitrocellulose, cyclohexanes, and castor oil.
The temperature of finished paint coating is to drop from 72 degrees to 27 degrees centigrade to be put to industrial uses.
Results
Castor oil was obtained simply by distillation. Also, the crude sample was tested. They were within acceptable industrial standards.
Castor oil incorporation as a plasticizer prevents cracks and corrosions. It improves the aesthetic looks of vehicles.
Performed experiments establish that the presence of ricinoleic acid, palmitic acid, and oleic acids indicate good quality.
Conclusion
Castor oil manufacturers in India brought a revolutionary change by putting this very bio-friendly substance to use in automotives.
Its industrial purpose was to limit corrosion and form a sturdy film externally. Also, polymer plasticizers were gradually being replaced by castor oil suppliers.
Today new polymers like resin and amino acids have taken over. They form the base of a diverse coating system, to say the least.